Outburst hazard zones of rock and gases in the Polish Coal Mining
Industry were mainly located in the Lower Silesia Coal Basin (closed
in the 90ties) in the mines: "Nowa Ruda", "Victoria", "Thorez", "Wałbrzych", "Cezar-Zofia" and "Wacław".
Usually, outburst was composed of coal and CO2, coal and
CH4, rock and CO2 or only gases.
In the salt mines ("Inowrocław" and "Kłodawa")
outbursts were less frequent. However, outbursts of salt and CH4,
salt and gases (CH4, H2S and N2) were
recorded.
In the Upper Silesia Coal Basin where mainly methane is accumulated
in a coal bed the last outburst was recorded in September of 2002 at
the Pniowek Coal Mine (no deaths).
Outburst at the Lower Silesia Coal Basin
In the Upper Silesia Coal Basin where mainly methane
is accumulated in a coal bed the last outburst was recorded in September
of 2002 at the Pniowek Coal Mine (no deaths).
The first recorded outburst in the Lower Silesia Coal
Basin occurred on 18.09.1894 at the ÒCezar-ZofiaÓ Coal Mine in the seam
nr 36 (presently nr 436) 80m deep. During the blasting preparation over
3 tones of coal followed by the CO2 outburst erupted.
The biggest Mine Disasters in Poland where outburst
occurred were mainly in the
Lower Silesia Coal Basin on 10.05.1941 at the "Nowa
Ruda" Mine – 187 deaths,
"Wacław" Mine on 9.08.1930 – 151 deaths,
"Nowa Ruda" Mine on 7.09.1976 – 18 deaths.

Causes of outburst:
-
high gas content of a coal bed
-
high rock mass pressure at the coal bed which is often intensified
by the mining activity
-
low strength of coal
Outburst Prevention in Polish Coal Mine Industry
Methods Applied in Polish Coal Mining Industry:
- De-stressing the coal seam
- Done by mining in advance of the adjacent seams which are
situated in a certain distance from the protected seams (de-stressed
seam)
-
By conducting in advance the parallel mining of adjacent
seams
The effectiveness of this method depends mainly on:
-
the distance between the coal seams
-
physical-mechanical properties of the rocks,
-
mining technology (roof control)
- Gas drainage.
This technique is mainly used while shaft sinking.
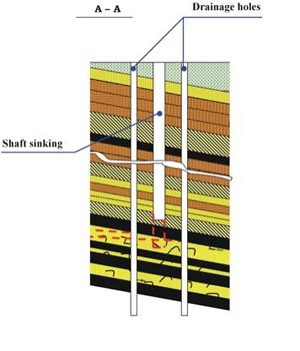
Fig. 1 Bore-hole gas drainage from the surface
- Water injection through the bore-hole from the surface
- Water injection into coal seam through shallow directional drilling
- Water injection into coal seam through deep directional drilling
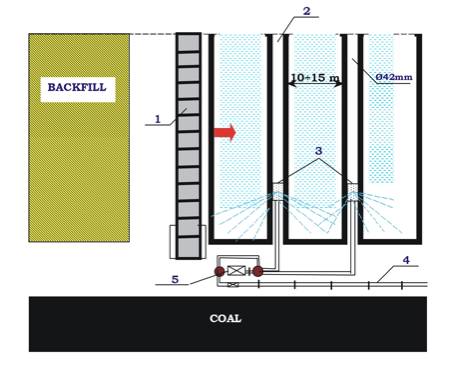
Fig. 2. Water injection into coal seam through deep directional drilling
(1. Conveyor 2. hole 42 mm (dia.) 3. water injection head 4. pipeline
5. pumping unit )
-
Hydro mining - washing out the coal of coal seam up to 10m
from the face (pressure of 4,9 MPa). Then, the coal seam is
drained and the coal is removed.
- Directional degassing and de-stressing directional drilling
- In the Lower Silesia Coal Basin small-diameter drilling of f
42 mm was used. Sometimes, the holes were enlarged to the diameter
of 110mm (or even more). The length of a hole was up to 15m. The
holes were drilled perpendicularly to the face, every 3 to 5 meters.
- Coal face blasting - de-stressing the coal seam
In the former mines of Lower Coal Silesia Basin the holes of 6 to
8m long were drilled. The blasting agent of 3 to 4 kg per 1 m of a
hole was placed. The purpose of this method was to de-stress the front
face of the coal seam by coal bursting and degassing the coal seam.
Prepared by:
Jan Palarski
Marcin Lutynski
Rafał Jendrus